A large part of steel produced is cast iron ingots and bars. Further processing then takes the for of forging, rolling or extrusion.
In monoblock casting, the molten steel is poured into moods. In continuous casting, the metal is cast in an open water cooled mold. Losing heat in the mold, the steel solidifies and is lowered in the form of a bar between holding and supporting rollers (pinch roll). The lowering speed can be up to 2 m/min. The high speed of solidification of the bars hinders segregation and the formation of gas cavities or shrinkage cavities, resulting in greater uniformity of structure.
After the development of continuous casting the older practice of cogging (rolling ingots derived from static moulding after heating them to incandescence in a crucible furnace) has been rendered obsolete. The bar cross sections can be adjusted to suit the shape of the finished product for which the steel is destined, reducing the extent of subsequent forming work required.
Casting materials
Casting materials are iron carbon alloys with around 2% to 4% carbon, whose properties suit them for the production of shaped casting.
Some materials falling into this category are: cast iron with lamellar graphite (GG), cast iron with nodular graphite (GGG), chilled iron (GH), malleable cast iron (GTW and GTS). These are melted in foundry shaft furnace.
Find here articles about carbon sheet, hard steel, stainless steel, stainless sheet, hard carbon, steel sheet, alloy sheet, alloy metal, stainless metal, carbon metal, sheet metal
How to Joint Iron without Welding
Joining iron without being welded is nothing new but usually the result is not as strong as if it were connected by welding. We can connect...
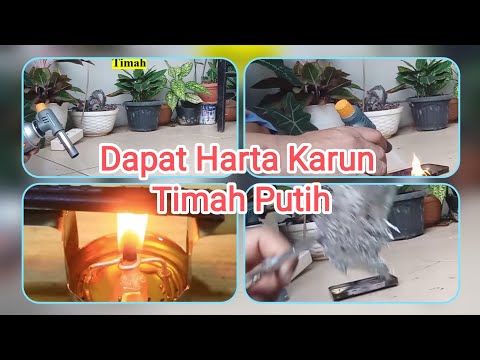
-
Steel Dimension and Type Steel Dimensions, weights, and properties of these sections are given by American Institute of Steel Constructi...
-
Carbon Steel Definition It is important to clarify the meaning of carbon steel in the generic sense and in the more narrow context use...
-
Carbon Steel Limit Allowable Stress The Code-allowable stresses are determined by the ASME Subcommittee on Materials and are listed in AS...